Why Reorder Point Can Hurt Your Business?
Maintaining proper inventory levels is the factor that must be balanced between consumer demand and supplier reliability in every business. If you store too much inventory, then it will eat up your budget, including warehousing fees and available capital.
In contrast, if you don’t have enough inventory, then you will have to account for unpredicted needs or supply problems. Also, it is a common problem for every manufacturing business to face some questions like How many kinds of stuff will I need to order from my supplier? When do I need to start my following supply order? Or, When do I have to create a new manufacturing order?
If you are the one who finds difficulties getting the right answer for these questions, there is a way to help you out, which is a reorder point calculation. Reorder points will make sure you don’t fall back compared to your next batch of inventory. Whether you have just begun a new business or have exchanged products for a while, you can still benefit from utilizing the reorder point formula method.
This post will show you what that is, why it is useful, and how to put those numbers together to ensure that you have the right amount of stock and safety stock and how to generate a reorder point. Let’s get started!
What is Reorder Point?
A reorder point is the unit quantity that provokes the purchase of a preset amount of replenishing inventory. In case the buying process and provider fulfillment work as planned, the reorder point should cause the replenishment inventory arriving when the last of the on-hand inventory is over.
As a result, there will be no interruption in manufacturing and fulfillment activities; at the same time, it can minimize the total number of inventory.
Overall, a reorder point is a stock threshold that you don’t want to go below. Meanwhile, the ideal inventory reorders point enables for a suitable time to place a new order before your stock extends to this threshold. For every item of inventory, the reorder point can be different because it may have a variety of usage rates and may need different amounts of time to acquire a provider’s replenishment delivery.
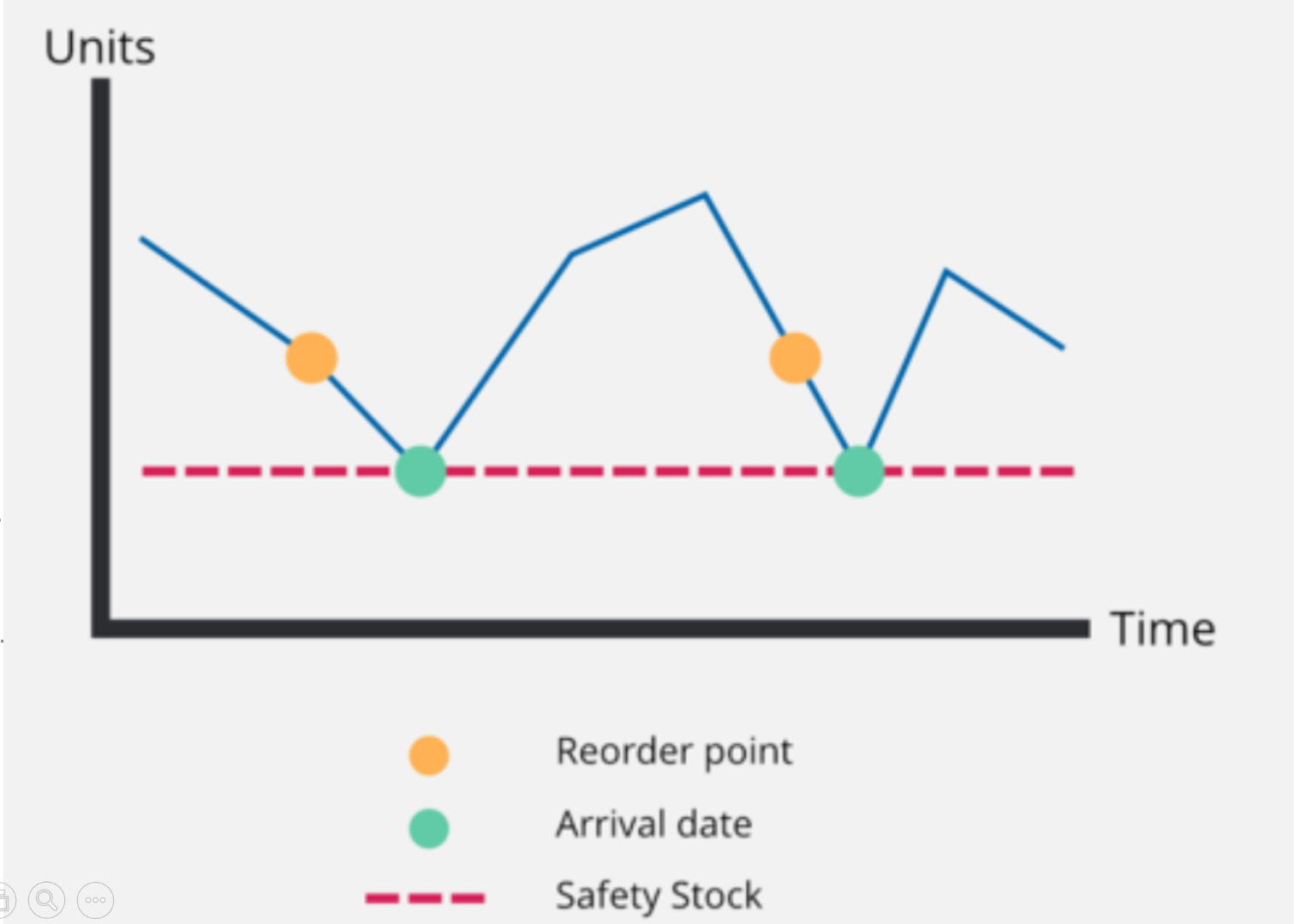
For instance, a company can pick and decide to purchase the same part from two separate suppliers. If one supplier needs one day to carry order and the other supplier says it needs three days, then the time for the company’s reorder point for the first supplier would be when there is one day’s stock left on hand or three days’ stock for the second supplier.
With the reorder point, your stock will be managed much better with reorder point, with fewer interruptions like supply-chain breakdowns or production congestions. Because when we look at the reorder point, we can see the metric that tells us two important things:
- When it is the right time to order more materials from your provider(s); and
- When it is the right time to produce more goods by generating a manufacturing order (MO).
Read more:
- Basic Google Tag Manager Tutorial for Digital Marketer
- Vertical market: How to serve a customer’s specific need?
- What is Performance Marketing?
- Attraction Marketing Definition
Why You Should Care About Reorder Point
The most obvious reason you should care about reorder points is that as your business develops, you will have to take care of more goods and SKUs. At the same time, the more challenging it will become to maintain your ideal stock levels. Then, your inventory reorder point levels should have every product in your inventory, like all of your product variation’s product recipe.
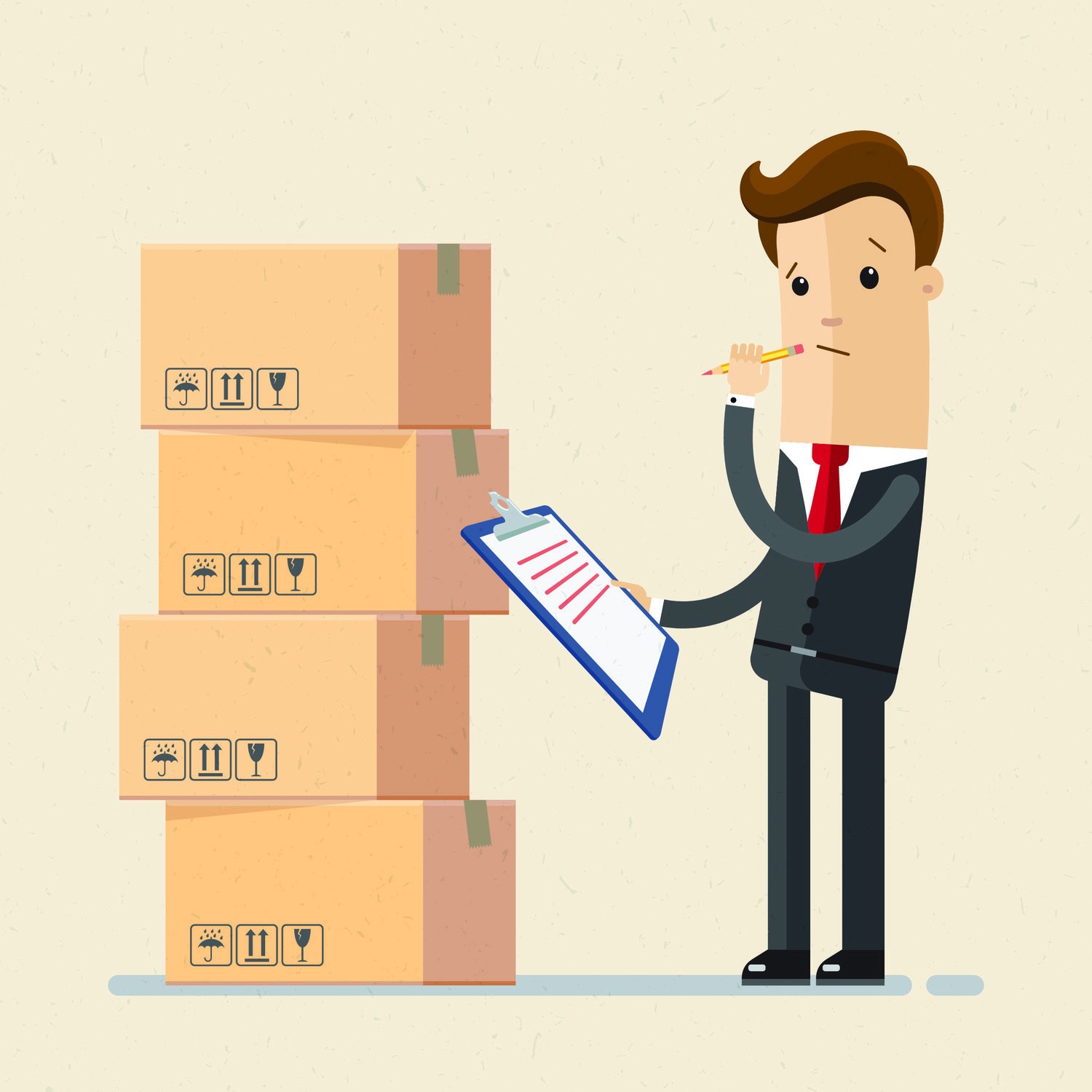
The reorder point is here to make sure that you don’t fall back on your next batch of inventory. If you have an exact reorder point for each SKU, you will always have enough stock on hand to please your customer requirements without having to tie up the excess capital in inventory. There are 3 main advantages of Reorder Point that I think will be effective for your business:
-
Minimize costs: When you store more inventory than the number of these can be sold in a timely fashion, then you can not get a productive use of capital. With reorder points, businesses will be provided with larger financial flexibility by enabling them to maintain the minimum amount of inventory on hand without running out of goods.
-
Minimize stockouts: When you have too much expensive inventory, however, too little inventory resulting in stockouts, then your business would be so harmful. It is when orders will be delayed or canceled, as a consequence, your business will lose customers, and your reputation can be damaged from this. With reorder points, you will be helped in preventing stockouts in the first place.
-
Better forecasting: Lastly, when you can calculate, reorder points will go hand in hand with creating an understandable idea of purchasing trends over a specific period. The more clearly that you calculate ROP for every item, the more correctly you can predict the users’ demand in the future and make sure that you use the reorder quantity formula accurately.
How to Calculate Reorder Point
To calculate the reorder point, there are three main steps that you should follow:
- Determine your lead time demand in days.
- Determine your safety stock in days.
- Sum your lead time demand and your safety stock to calculate your Reorder Point.
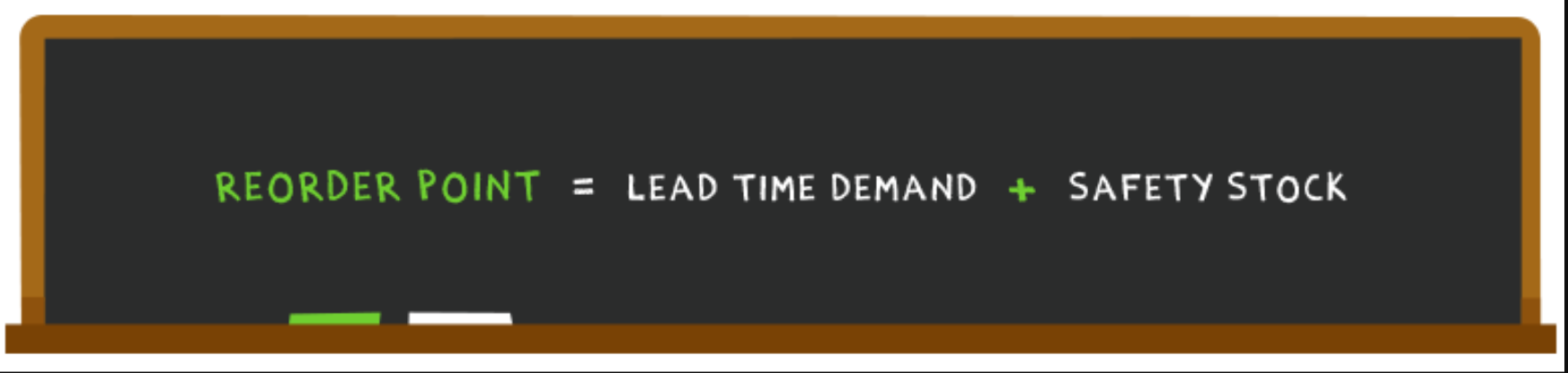
Here is the formula after you have determined all three elements: Reorder Point = Lead time demand + Safety Stock
You will reorder before it goes out of stock, however, if you order too soon, you will have to pay more money on storing these excess goods. In case you are too late for ordering, you will be more likely to face disappointed users who’ll look to your competitors.
So, the question that was asked by most people is: When is the right time to order more stock?
To help you out, I have a formula provided for determining to reorder point, which will let you know exactly the time you should place an order for a new shipment of products:
Lead time in days (Time it takes for a bought order from a provider to arrive) x Average daily usage (Average number of units of an item that you sell a day) + Safety stock
Let’s break this formula down and look at the math: Firstly, you will have to know the lead time demand, which is the time that you will have to wait before new stock arrives. This will help you have enough time to please your customers while waiting. Also, you should know about your safety stock, which will keep you safe from any unexpected occurrences. Once your stock levels hit the total, then it’s high time to set a new order to fill up your supply again.
Reorder Point and Safety Stock
Unpredictable things happen sometimes, which can be when there is a sudden surge in demand on your pieces of stuff after some unexpected celebrity endorsement, or this can be when your supplier’s factory broke down and it requires a week for them to fix the damaged component and take it back to normal again. And here’s the time that you need safety stock to help you.
Safety stock is buffer stock carried as a last defense against unexpected events including these consume your stock (surge in demand), or unforeseen manufacturing program (your lead time soar due to the breakdown supply chain). So, safety stock is something that you would like to own enough to help you bring the tendency of going out of stock down to zero, but if you don’t carefully calculate it, then most of the time it will not be financially viable for your business.
That’s why I have created a short part to instruct you on how we decide on how much stock to keep. Let’s see!
Here’s a simple formula that you use to calculate referring to the number of your purchase and sales orders history:
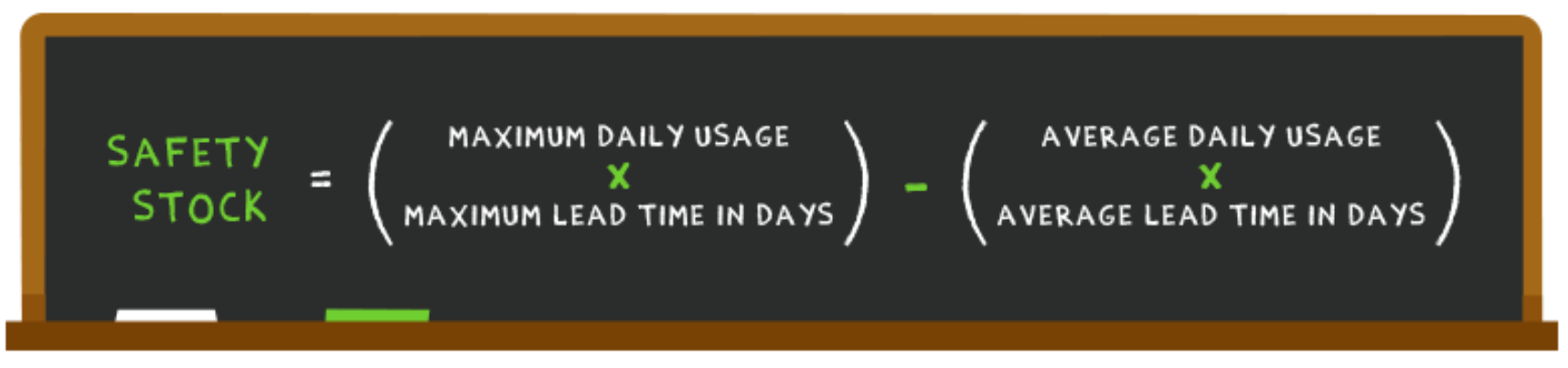
There was a story of J Timewear, whose business sells an average of 10 watches per day. And during weekends, they can sell about 15 items. Plus, their usual lead time is 47 days, but when typhoon season comes, it can go up to 54 days. To sum up, we have this calculation: (15 x 54) - (10 x 47) = 340
Hence, J Timewear will have to own 340 units of safety stock on hand to avoid risk from unexpected events. If they have 340 units in safety stock, they will be able to sell 80 watches on a good week (10 per day on weekdays and 15 on weekends), which can help J Timewear to have enough stock to last over 4 weeks.
If you are selling a seasonal product, like school supplies, you will have to change your safety stock level in case of peak season demand. Once the peak season has passed, then you can decide to reduce your safety stock levels because more safety stock means higher carrying costs. To conclude the case of J Timewear, their reorder point formula calculation would be: 470 (Lead time demand) + 340 (safety stock) = 810
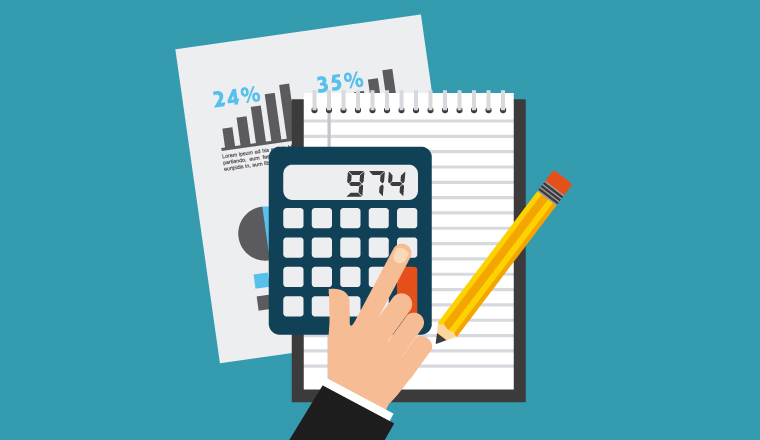
So, you can see why planning reorder points are so important for business’ inventory management. If you can set your reorder point to the optimum amount, you will be able to cut down a part of excess spending while still making sure that you will have enough stock for your customers when there is an unexpected turn.
I’m sure that you don’t want to place your products on the backorder and tell your customers “Oh, I’m sorry, we are out of stock and we can’t get new stock for another week” and make them disappointed. So, it’s never too late to start calculating and managing your Reorder Point and Safety Stock for your business!
Related posts:
- Customer engagement for eCommerce
- Mass Marketing 101
- How to implement Proximity Marketing
- What is a vertical marketing system?
- Growth Marketing: Definition, Best Practices, and Examples
Conclusion
After all, your reorder point is a key factor, together with safety stock, to be components of the larger scheme of inventory management and your supply chain. It is necessary to implement your own reorder point strategy to make sure that your business is running at maximum efficiency across inbound and outbound logistics. This may not help you address the whole puzzle, but the reorder point can offer you a more accurate basis for your stock replenishment schedule.
Also, the most crucial and maybe hardest part of calculating reorder points concisely is that you must have reliable data throughout your supply chain and accurate picture of customer demand. In case your data is off, the calculation will become incorrect and you will soon end up with too much or too little stock. So, be aware of that!
That wraps my article today for Why Not Knowing About Reorder Point Can Hurt Your Business! I hope you will find something helpful in my post today, which will contribute a bit to your business’s success. If there is still something you don’t understand about market orientation or want to know more about it, please let us know via the comment section.
We are looking forward to hearing from you!
New Posts